Introduction
In the world of manufacturing, the significance of a quality wire forming machine cannot be overstated. These machines are the backbone of countless industries, producing everything from intricate custom wire forming and wire fasteners to robust components that stand the test of time. With advancements in technology, the landscape of wire bending machines has evolved, offering solutions that enhance efficiency and precision like never before.
The Importance of a Quality Wire Forming Machine
A quality wire forming machine is essential for ensuring consistent production and high-quality output. When manufacturers invest in reliable equipment, they not only improve their product integrity but also streamline their operations, ultimately saving time and resources. The right machine can make all the difference between a successful project and one riddled with defects or delays.
Understanding Custom Wire Forming & Wire Fasteners
Custom wire forming involves tailoring products to meet specific needs, which often requires specialized machinery capable of intricate designs. Wire fasteners play a crucial role in assembly processes across various sectors, providing secure connections that keep products together seamlessly. By understanding these elements, businesses can better appreciate how investing in advanced technologies like CNC wire bending machines can elevate their offerings.
Innovations in Wire Bending Machines
The evolution of wire bending machines has brought forth innovative features that enhance functionality and usability. From CNC wire bending machines for sale to automated systems designed for complex tasks, manufacturers have access to tools that were once unimaginable. These innovations not only improve precision but also enable faster production times while reducing waste—making them indispensable in today’s competitive market.
Overview of Wire Forming Technology

Wire forming technology has evolved significantly, providing manufacturers with enhanced capabilities to create intricate designs and components. A quality wire forming machine is essential for producing custom wire forming and wire fasteners that meet the specific needs of various industries. Understanding the different types of machines and their applications can help businesses optimize their production processes.
Types of Wire Forming Machines
There are several types of wire forming machines available on the market, each designed to cater to specific manufacturing requirements. CNC wire bending machines, for instance, offer precision and automation, making them ideal for high-volume production runs. On the other hand, manual wire bending machines provide flexibility and control, allowing operators to create custom designs with ease.
Spring wire forming machines are another specialized category that focuses on creating springs and other similar components. These machines can handle various wire sizes and materials, ensuring versatility in production. By understanding the different types of wire forming machines available, manufacturers can select the right equipment that aligns with their operational goals.
Applications of Wire Forming
Wire forming technology finds applications across a wide range of industries, from automotive to aerospace and beyond. Custom wire forming & wire fasteners are used in everything from assembling vehicles to constructing buildings, showcasing the versatility of these products. Additionally, industries such as electronics rely heavily on precise wire forms for connectors and other critical components.
In healthcare settings, medical devices often incorporate specialized wire forms that require both precision and reliability. The ability to produce intricate shapes quickly makes quality wire forming machines indispensable in today’s fast-paced manufacturing environments. As demand grows for customized solutions across sectors, understanding these applications becomes crucial for manufacturers aiming to stay competitive.
Benefits of Advanced Wire Forming Techniques
Advanced wire forming techniques offer numerous benefits that can significantly enhance production efficiency and product quality. Utilizing a CNC wire bending machine for sale can lead to reduced labor costs while increasing output consistency due to automated processes. Moreover, these advanced techniques enable manufacturers to achieve tighter tolerances and more complex geometries than ever before.
Another advantage lies in material savings; by optimizing designs through advanced software integrated into modern machines like spring wire forming machines or CNC setups, companies can reduce waste significantly during production runs. Furthermore, investing in a quality wire forming machine means improved durability and performance characteristics in finished products—key factors when competing in demanding markets.
Overall, embracing innovative technologies within the realm of custom wire forming not only boosts operational efficiency but also enhances product offerings across diverse industries.
The Role of CNC Wire Bending Machines
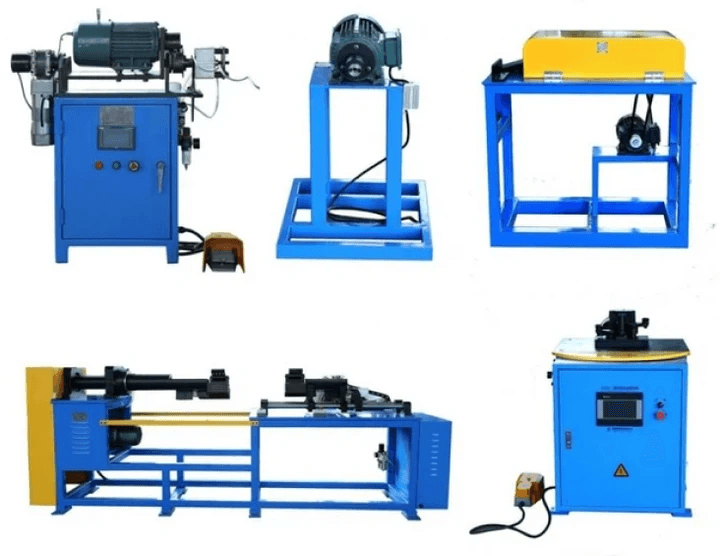
CNC wire bending machines have revolutionized the manufacturing landscape, providing an efficient and precise way to produce custom wire forming and wire fasteners. These machines utilize computer numerical control technology to automate the bending process, allowing for intricate designs that would be nearly impossible with manual wire bending machines. As industries continue to demand higher standards of quality and precision, the role of CNC technology in wire forming becomes increasingly vital.
Advantages of CNC Technology
One of the standout advantages of CNC technology is its ability to enhance productivity in manufacturing environments. A quality wire forming machine equipped with CNC capabilities can operate continuously, producing consistent results without fatigue or error—a significant upgrade over manual wire bending machines. Additionally, these machines can easily switch between different designs, making them perfect for businesses that require custom wire forming & wire fasteners for various applications.
Another key benefit is the reduction in labor costs associated with operating a CNC wire bending machine. With automation handling most tasks, companies can allocate human resources to more complex jobs that require critical thinking and creativity. This shift not only optimizes workflow but also ensures that skilled workers are utilized where they are needed most.
Precision in Wire Forming Processes
Precision is paramount when it comes to creating high-quality products with a quality wire forming machine. CNC technology allows manufacturers to achieve tight tolerances and repeatable accuracy in their designs, which is crucial for components used in sectors like automotive and aerospace where safety is non-negotiable. The ability to program specific measurements into a CNC wire bending machine means that every piece produced meets exact specifications without deviation.
Moreover, this precision minimizes material waste during production—another win-win for both manufacturers and the environment. By ensuring accurate cuts and bends from the start, companies can maximize their raw materials while also reducing costs associated with leftover scrap metal from less precise methods like manual bending. This efficiency not only saves money but also aligns with sustainable practices increasingly demanded by consumers today.
Leading CNC Wire Bending Machines on the Market
When it comes to investing in a CNC wire bending machine for sale, several brands stand out due to their reliability and performance features tailored for various industries' needs. Companies like WAFIOS offer advanced models known for their versatility in handling different types of wires while maintaining exceptional build quality—a must-have trait for any quality wire forming machine on the market today. Other notable names include KUKA and TRUMPF, which provide robust solutions designed specifically for high-volume production.
In addition to brand reputation, it's essential to consider factors such as user-friendly interfaces and support services when choosing a machine. Many leading manufacturers now focus on integrating smart technologies into their products—think IoT connectivity—that allows operators real-time monitoring and troubleshooting capabilities right from their devices! Investing wisely here can significantly impact operational efficiency down the line.
Manual Wire Bending Machines

When it comes to wire forming, manual wire bending machines hold a special place in the hearts of craftsmen and small manufacturers alike. These machines offer a hands-on approach that can be appealing for those who appreciate the artistry behind custom wire forming & wire fasteners. However, while they provide flexibility and control, they also come with their own set of challenges that must be considered.
Pros and Cons of Manual Machines
One of the major advantages of manual wire bending machines is their affordability compared to automated options like CNC wire bending machines. They require less initial investment, making them accessible for startups or hobbyists looking to experiment with custom designs. However, this cost-effectiveness comes at a price: manual machines often lack the precision and speed that modern automated systems provide, which can lead to inconsistencies in production.
On the flip side, manual machines allow for greater creative freedom and adaptability when it comes to custom projects. Users can easily adjust their techniques on-the-fly without needing complex programming or software updates associated with advanced CNC technology. Nevertheless, this flexibility may result in longer production times and increased physical strain on operators who are manually handling materials.
Comparing Manual vs. Automated Options
When comparing manual wire bending machines to their automated counterparts like CNC wire bending machines for sale, it's essential to consider factors such as volume, precision, and skill level required. Automated systems excel in high-volume production settings where uniformity and speed are paramount; they can churn out thousands of identical pieces in no time at all. In contrast, manual options shine when it comes to low-volume or one-off projects requiring intricate details or unique designs.
Moreover, while a quality wire forming machine might automate tedious processes effectively, it often requires skilled personnel for setup and maintenance—something that could be daunting for smaller businesses or individuals just starting out with spring wire forming machine applications. Conversely, anyone with basic skills can operate a manual machine after some practice; this democratizes access to wire forming technology but may compromise efficiency over larger runs.
Ultimately, the choice between manual and automated options should align with your specific needs—whether you prioritize artistic expression over mass production or vice versa.
Best Practices for Using Manual Wire Benders
To get the most out of your manual wire bending machine while ensuring safety and efficiency, adopting best practices is crucial. First off, always keep your workspace organized; clutter can lead to accidents or mistakes during intricate bends required for custom wire forming & wire fasteners projects. Additionally, regularly inspect your tools for wear-and-tear—sharp edges on benders should be maintained properly to ensure clean cuts.
Another key practice is mastering proper techniques before diving into complex designs; start small! Familiarize yourself with different types of bends (like loops versus angles) before attempting elaborate shapes commonly found in spring wire forming machine applications. This foundational knowledge will pay dividends as you gain experience over time.
Finally—and perhaps most importantly—always prioritize safety by wearing appropriate protective gear such as gloves and goggles during operation! While these measures may seem tedious at first glance when working with a quality wire forming machine like a manual bender becomes second nature over time.
Spotlight on Spring Wire Forming Machines
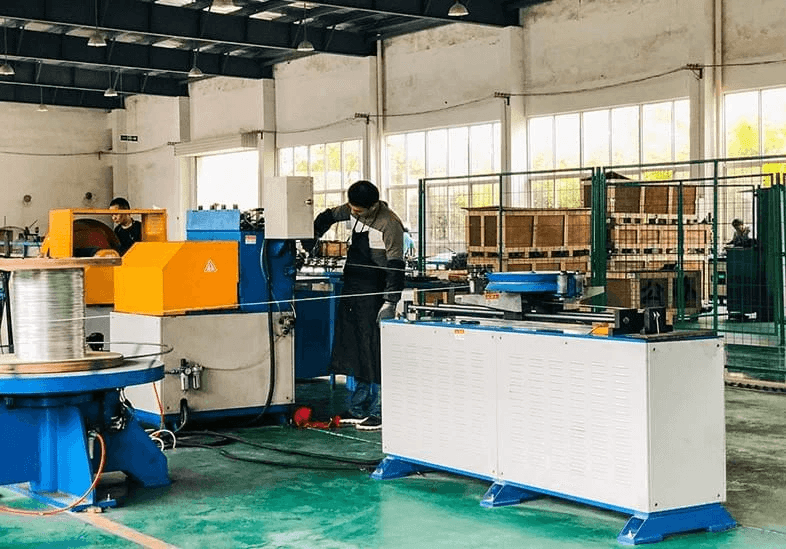
When it comes to wire forming, spring wire forming machines are the unsung heroes of precision and efficiency. These specialized machines are designed to create intricate shapes and forms from wire, making them indispensable in various industries. Whether you're looking for a quality wire forming machine for large-scale production or custom solutions, spring wire forming machines offer unique features that elevate your manufacturing game.
Unique Features and Benefits
Spring wire forming machines stand out due to their advanced capabilities and versatility. They can produce complex shapes with high precision, making them ideal for Custom Wire Forming & Wire Fasteners applications where exact specifications are crucial. With options ranging from CNC Wire bending machines to manual wire bending machines, manufacturers have the flexibility to choose a solution that best fits their operational needs while ensuring top-notch quality.
Another significant benefit is their ability to handle various materials, including stainless steel and copper alloys. This adaptability allows businesses to expand their product offerings without investing in multiple types of equipment. Furthermore, the integration of automation technology enhances production speed while maintaining accuracy—an essential factor for staying competitive in today's fast-paced market.
Common Applications in Various Industries
Spring wire forming machines are utilized across a broad spectrum of industries due to their unique capabilities. In the automotive sector, they are essential for producing components like springs and brackets that require both strength and flexibility. Similarly, they play a crucial role in the electronics industry by creating intricate parts such as connectors and clips that ensure devices function seamlessly.
Moreover, these machines are vital in manufacturing household items like furniture springs or appliance components where durability is key. The versatility of spring wire forming allows manufacturers to cater not only to mass production but also to Custom Wire Forming & Wire Fasteners projects tailored for specific client needs. As such, industries ranging from aerospace to medical devices benefit immensely from these advanced solutions.
Top Brands Offering Spring Wire Forming Solutions
When searching for a reliable spring wire forming machine, several brands consistently lead the market with innovative offerings. Companies like Hines Industries and WAFIOS provide top-of-the-line equipment known for durability and precision—essential attributes when investing in a quality wire forming machine. Additionally, brands such as KUKA Robotics have made strides by integrating CNC technology into their designs, offering CNC Wire bending machines for sale that promise unmatched performance.
Another notable mention is TJK Machinery which specializes in customizable solutions suitable for both small-scale operations using manual wire bending machines or larger automated setups designed for high-volume production runs. By choosing reputable brands known for their commitment to quality and innovation, businesses can ensure they’re equipped with machinery capable of meeting evolving industry demands while achieving superior results.
The 16A Pre-Twisted Wire Automatic Forming Production Line
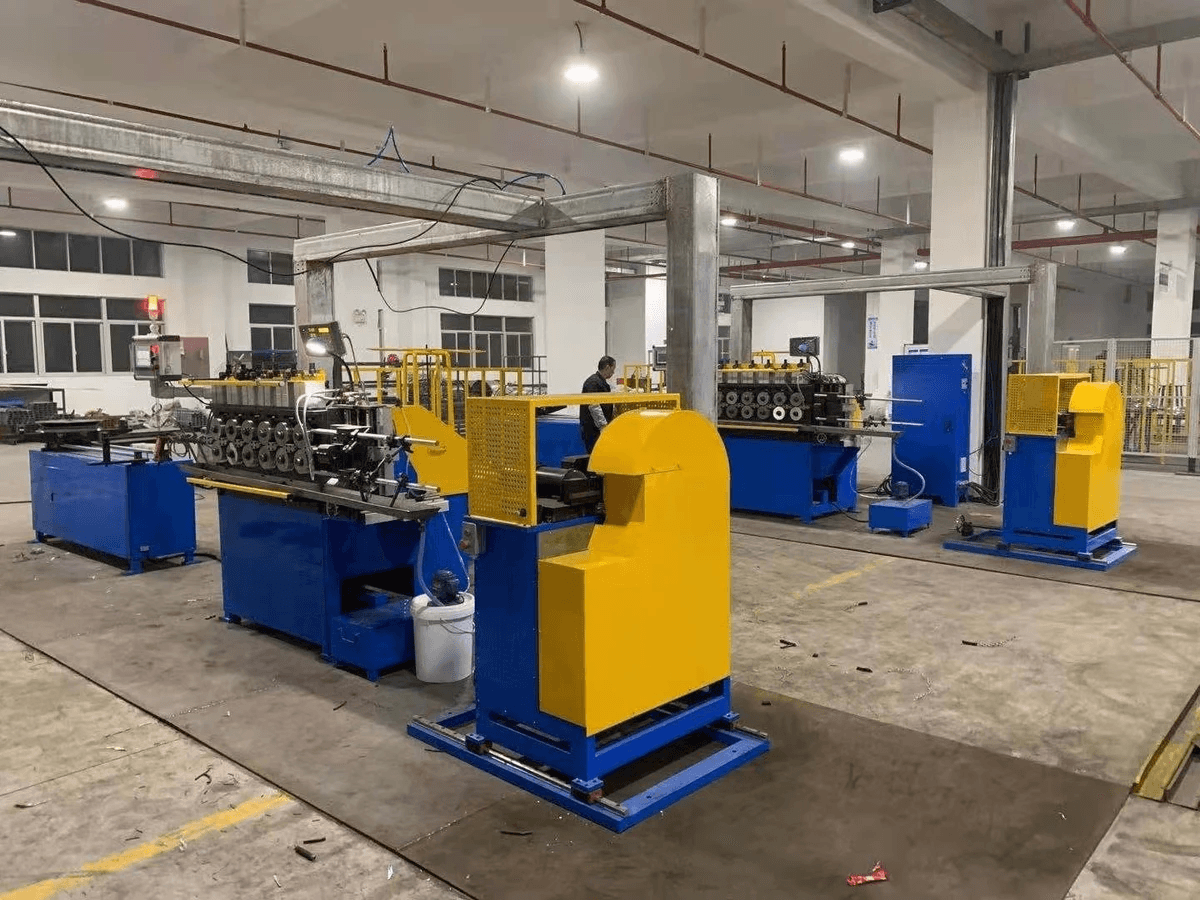
In the realm of wire forming technology, the 16A Pre-Twisted Wire Automatic Forming Production Line stands out as a game-changer. This innovative system is designed to streamline the production of custom wire forming and wire fasteners, ensuring high-quality output with minimal labor. By integrating advanced features, this line enhances both efficiency and precision in wire bending processes.
Features of the Spark Fittings Production Line
The Spark Fittings Production Line boasts an array of impressive features that make it a top choice for manufacturers seeking a quality wire forming machine. It includes programmable controls that allow for easy adjustments to accommodate various specifications in custom wire forming and wire fasteners. Additionally, this line is equipped with robust safety features and user-friendly interfaces, making it accessible even for operators familiar with manual wire bending machines.
Another standout feature is its ability to handle multiple types of materials, including different gauges of spring steel and other metals commonly used in spring wire forming machines. This versatility ensures that businesses can adapt quickly to changing market demands without investing in new equipment constantly. Furthermore, its automated feeding system minimizes material waste while maximizing production speed—an essential factor for any competitive manufacturing operation.
How It Enhances Efficiency and Precision
The 16A Pre-Twisted Wire Automatic Forming Production Line significantly enhances efficiency through automation, reducing the need for manual intervention during production runs. This means fewer errors typically associated with manual wire bending machines, leading to higher precision in every piece produced. Moreover, the CNC technology integrated into this system allows for intricate designs that would be challenging to achieve with traditional methods.
By optimizing workflows and minimizing downtime between setups, this production line dramatically increases output rates while maintaining quality standards expected from a leading CNC wire bending machine for sale. The result is not only faster turnaround times but also consistent quality across all products—essential when dealing with custom requirements in various industries. Businesses can now meet tight deadlines without compromising on quality or precision.
Real-World Applications and Case Studies
Real-world applications of the 16A Pre-Twisted Wire Automatic Forming Production Line span numerous industries such as automotive, aerospace, and electronics where custom wire forming and wire fasteners are crucial components. For instance, one automotive manufacturer reported a 30% increase in productivity after implementing this automated solution compared to their previous manual processes using standard manual wire bending machines.
Case studies reveal that companies utilizing this advanced technology have successfully reduced material waste by up to 25%, translating into significant cost savings over time—a benefit not overlooked by savvy business owners looking at their bottom line! Additionally, clients have praised the consistency achieved with each batch produced; no more variations or defects typically seen when relying solely on less sophisticated machinery.
Conclusion
In the ever-evolving landscape of manufacturing, the choice of a quality wire forming machine can significantly influence production efficiency and product quality. Whether you're venturing into custom wire forming & wire fasteners or exploring advanced CNC technologies, understanding your options is crucial. With a variety of machines available—from manual wire bending machines to sophisticated CNC wire bending machines for sale—selecting the right equipment tailored to your needs ensures optimal performance.
Choosing the Right Wire Forming Machine
Custom wire forming & wire fasteners often require specialized equipment that can adapt to various specifications and designs. By weighing the pros and cons of manual vs. automated options, you can make an informed decision that aligns with your operational goals.
Prioritizing Efficiency and Precision
Efficiency and precision are paramount in modern manufacturing environments where every second counts. Investing in advanced technologies like CNC wire bending machines enhances both speed and accuracy in producing complex shapes and forms. Additionally, a well-chosen spring wire forming machine can streamline processes while ensuring high-quality outputs that meet industry standards.
Future Trends in Wire Forming Technology
The future of wire forming technology is poised for exciting advancements driven by automation, artificial intelligence, and smart manufacturing practices. As manufacturers seek more efficient solutions, innovations in CNC technology will likely lead to even more precise and versatile applications for custom wire forming & wire fasteners. Staying abreast of these trends will enable businesses to remain competitive while optimizing their use of quality wire forming machines.