Introduction
In the world of manufacturing, transmission wireform manufacturing stands out as a critical component in various industries. These specialized wire forms play an essential role in everything from automotive applications to electronics, ensuring that products function efficiently and reliably. Understanding the nuances of wire form manufacturers is vital for businesses looking to optimize their supply chains and enhance product quality.
Understanding Transmission Wireform Manufacturing
Transmission wireform manufacturing encompasses the creation of intricate shapes and structures from metal wires, tailored to meet specific operational needs. This process involves precision engineering and a keen understanding of material properties, resulting in wire forms that can withstand diverse environmental conditions. As industries continue to evolve, the demand for skilled wire form manufacturers grows, highlighting the importance of expertise in this niche sector.
Importance of Quality Wire Forms
Quality wire forms are not just a luxury; they are a necessity for ensuring safety and performance in various applications. Poorly manufactured wire forms can lead to catastrophic failures, affecting both functionality and safety standards across industries. Therefore, choosing reliable wire form suppliers who prioritize quality control is paramount for any business aiming to maintain high operational standards.
Overview of Leading Manufacturers
The market is home to several leading transmission wireform manufacturers known for their commitment to quality and innovation. These companies leverage advanced technologies and skilled craftsmanship to produce superior wire forms that cater to diverse industry needs. By exploring these top-tier manufacturers, businesses can gain insights into best practices and emerging trends that shape the future of wire form production.
What are Wire Forms?
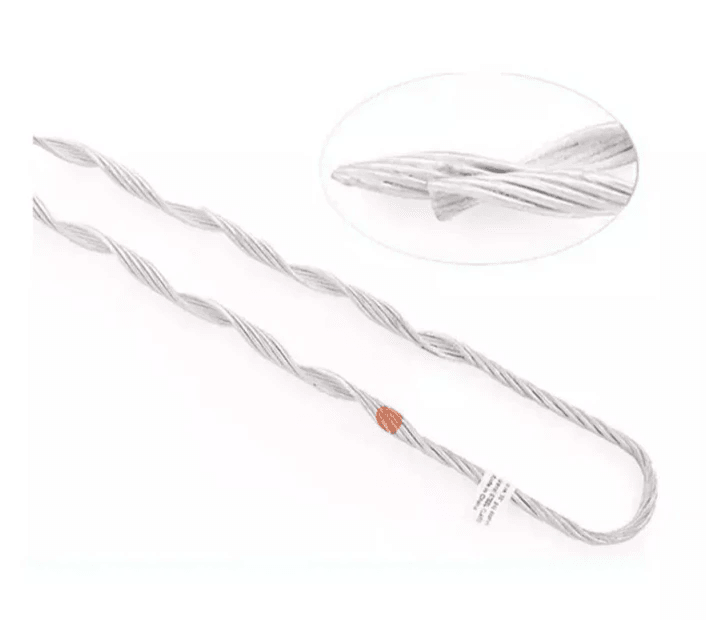
Wire forms are versatile components that play a crucial role in various mechanical applications. These elements, typically made from metal wire, can be shaped into numerous configurations to serve different functional purposes. From simple hooks to complex brackets, wire forms are essential in ensuring the efficiency of many products and systems.
Definition and Applications
At their core, wire forms are customized shapes created from wire materials, designed to meet specific functional requirements. Their applications span a wide range of industries, including automotive, aerospace, electronics, and construction. Transmission wireform manufacturers frequently produce these components to support structures like cable assemblies and harnesses that require precise geometry for optimal performance.
Types of Wire Forms
There is an impressive variety of wire forms available on the market today, each tailored for unique applications. Some common types include clips, brackets, springs, and custom-shaped parts designed for specific machinery or devices. Wire form manufacturers often collaborate with clients to develop specialized designs that fit their particular needs while adhering to industry standards.
Industries Utilizing Wire Forms
Wire forms find their place across multiple industries due to their adaptability and functionality. The automotive sector relies heavily on these components for everything from seat frames to electrical connectors—ensuring safety and reliability in vehicles on the road. Similarly, the aerospace industry utilizes high-quality wire forms manufactured by leading suppliers to meet rigorous performance standards required for flight safety and efficiency.
Key Players in Transmission Wireform Manufacturing
When it comes to transmission wireform manufacturing, a handful of companies stand out as leaders in the industry. These top wire form manufacturers not only produce high-quality products but also set the standard for innovation and reliability. Their commitment to excellence ensures that they remain at the forefront of this competitive market.
Overview of Top Wire Form Manufacturers
In the realm of wire forms, several manufacturers have gained recognition for their superior products and services. Companies like XYZ Wire Forms, ABC Manufacturing, and 123 Metalworks are known for their diverse range of offerings tailored to various industries. These transmission wireform manufacturers invest heavily in research and development, enabling them to create cutting-edge solutions that meet evolving customer needs.
The success of these top wire form manufacturers can be attributed to their focus on quality control and customer satisfaction. By adhering to stringent manufacturing standards and utilizing advanced technologies, they ensure that their wire forms are both durable and efficient. This dedication not only enhances their reputation but also fosters long-term partnerships with clients across multiple sectors.
Notable Wire Form Suppliers
Beyond the major players in manufacturing, there are several notable wire form suppliers who contribute significantly to the supply chain. Companies such as Fasteners Inc., WireWorks Supply Co., and Precision Wire Products offer a variety of specialized wire forms that cater to niche markets. These suppliers often collaborate closely with manufacturers to deliver customized solutions that meet specific client requirements.
Notable wire form suppliers play a crucial role in ensuring that raw materials are sourced responsibly while maintaining competitive pricing. Their extensive networks allow them to provide timely deliveries without compromising on quality or service reliability. As a result, these suppliers become indispensable partners for many transmission wireform manufacturers looking to enhance their product offerings.
Emerging Trends among Leading Companies
As the landscape of transmission wireform manufacturing continues to evolve, several emerging trends are shaping how leading companies operate within this space. One significant trend is the increasing adoption of sustainable practices among wire form manufacturers, driven by consumer demand for eco-friendly products. This shift not only helps reduce environmental impact but also attracts customers who prioritize sustainability in their purchasing decisions.
Another trend is the integration of advanced technologies such as automation and artificial intelligence into production processes. These innovations enable manufacturers to streamline operations, improve efficiency, and enhance product quality—ultimately leading to greater customer satisfaction among end-users seeking reliable wire forms from trusted sources.
Finally, collaboration is becoming more prevalent within the industry as companies recognize the value of partnerships with other organizations—be it fellow manufacturers or technology providers—to drive innovation forward collectively.
Essential Features of Quality Wire Forms
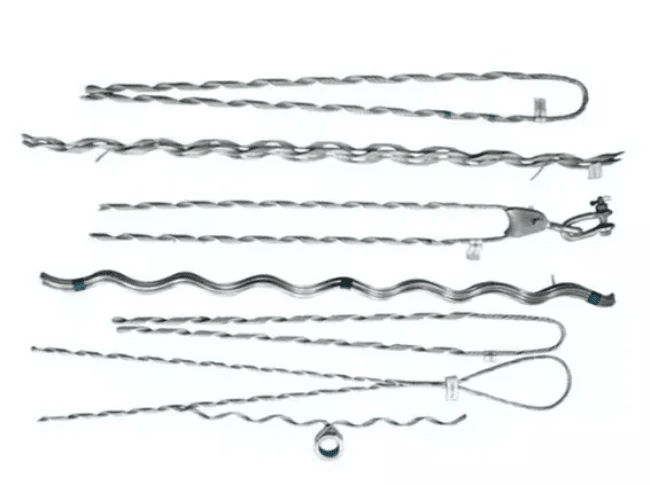
When it comes to wire forms, not all are created equal. The essential features that define quality wire forms can significantly impact their performance and longevity in various applications. Understanding these features is crucial for anyone looking to partner with reputable transmission wireform manufacturers or wire form suppliers.
Material Specifications and Standards
The foundation of any quality wire form lies in its material specifications and standards. High-grade materials such as stainless steel, aluminum, and specialized alloys are frequently used by leading wire form manufacturers to ensure durability and resistance to corrosion. Adhering to industry standards not only enhances the reliability of the wire forms but also ensures compliance with safety regulations across different sectors.
Selecting the right material is vital for specific applications; for instance, automotive industries often require lightweight yet strong materials, while aerospace applications demand exceptional strength-to-weight ratios. Transmission wireform manufacturers must be knowledgeable about these requirements to provide tailored solutions that meet client needs effectively. Ultimately, the choice of materials directly influences the performance characteristics of the final product.
Design Considerations for Durability
Design plays a pivotal role in determining how well a wire form will perform over time. Quality wire forms should incorporate design elements that enhance durability—think about factors like load distribution, stress points, and environmental exposure. Leading wire form suppliers utilize advanced design techniques such as finite element analysis (FEA) to predict potential failure points and optimize designs accordingly.
Moreover, thoughtful design can also simplify installation processes or reduce manufacturing costs without compromising quality. This is where collaboration between customers and transmission wireform manufacturers becomes invaluable; sharing insights can lead to innovative designs that maximize both functionality and longevity in diverse applications. In essence, robust design considerations are indispensable for ensuring that a product withstands rigorous use over its lifespan.
Performance Testing and Quality Control
No matter how great the materials or designs may be, performance testing is what truly validates the quality of a wire form. Rigorous testing protocols help ensure that each product meets predetermined standards before it reaches customers—this includes tensile strength tests, fatigue tests, and environmental simulations among others conducted by reputable wire form manufacturers. Such comprehensive quality control measures safeguard against defects that could compromise performance or safety.
Additionally, industry-leading suppliers often implement continuous improvement strategies based on feedback from these tests; this allows them to refine their processes continually while adapting to emerging market demands or technological advancements. Choosing a manufacturer who prioritizes thorough performance testing gives customers peace of mind knowing they are investing in reliable products designed for optimal efficiency over time. In summary, effective quality control measures are non-negotiable when it comes to producing top-tier wire forms.
Advancements in Wire Form Production
The wire form manufacturing industry is experiencing a seismic shift thanks to technological advancements that are revolutionizing production processes. With the rise of smart technologies, transmission wireform manufacturers are now able to produce wire forms with unprecedented precision and efficiency. This evolution not only enhances product quality but also streamlines operations, allowing manufacturers to meet the ever-increasing demand for specialized wire forms across various industries.
The Role of Technology in Manufacturing
Technology plays a pivotal role in modernizing the manufacturing landscape for wire forms. From computer-aided design (CAD) software that allows for intricate designs to advanced machinery equipped with robotics, transmission wireform manufacturers can create complex shapes and sizes with ease. Additionally, data analytics tools enable better inventory management and predictive maintenance, ensuring that production lines run smoothly without unexpected downtimes.
Moreover, additive manufacturing techniques such as 3D printing are making waves in the industry by allowing for rapid prototyping of wire forms. This not only reduces lead times but also facilitates customization, enabling wire form suppliers to cater to specific client needs efficiently. As technology continues to evolve, it’s clear that its integration into manufacturing processes is essential for staying competitive in the dynamic market of wire forms.
Innovations by Spark Fittings
Spark Fittings has emerged as a trailblazer among wire form manufacturers by introducing groundbreaking innovations that set new benchmarks in the industry. Their commitment to research and development has led to the creation of high-performance materials specifically designed for demanding applications in sectors like automotive and aerospace. These innovative materials enhance durability while reducing weight, making them ideal choices for modern engineering challenges.
In addition to material advancements, Spark Fittings has invested heavily in automation technologies that optimize their production capabilities. Their state-of-the-art facilities utilize robotic systems for precision bending and forming processes, significantly increasing production speed while maintaining high-quality standards. By embracing innovation at every level of their operations, Spark Fittings exemplifies how forward-thinking approaches can drive success among leading transmission wireform manufacturers.
Benefits of Automated Production Lines
The shift towards automated production lines represents a significant leap forward for both efficiency and quality control within the wire form sector. For transmission wireform manufacturers, automation minimizes human error while maximizing output—an essential combination when producing large volumes of complex components like custom wire forms. With machines capable of executing repetitive tasks with pinpoint accuracy, companies can ensure consistent quality across all products.
Furthermore, automated systems allow for real-time monitoring and adjustments during the manufacturing process; this results in reduced waste and optimized resource allocation—both crucial factors in today’s environmentally conscious market landscape. Wire form suppliers leveraging these advanced technologies can respond more swiftly to customer demands without compromising on quality or performance metrics—a win-win situation all around!
In conclusion, advancements in technology are reshaping how transmission wireform manufacturers operate today; embracing these changes is vital for anyone looking to stay ahead in this competitive field.
Choosing the Right Manufacturer
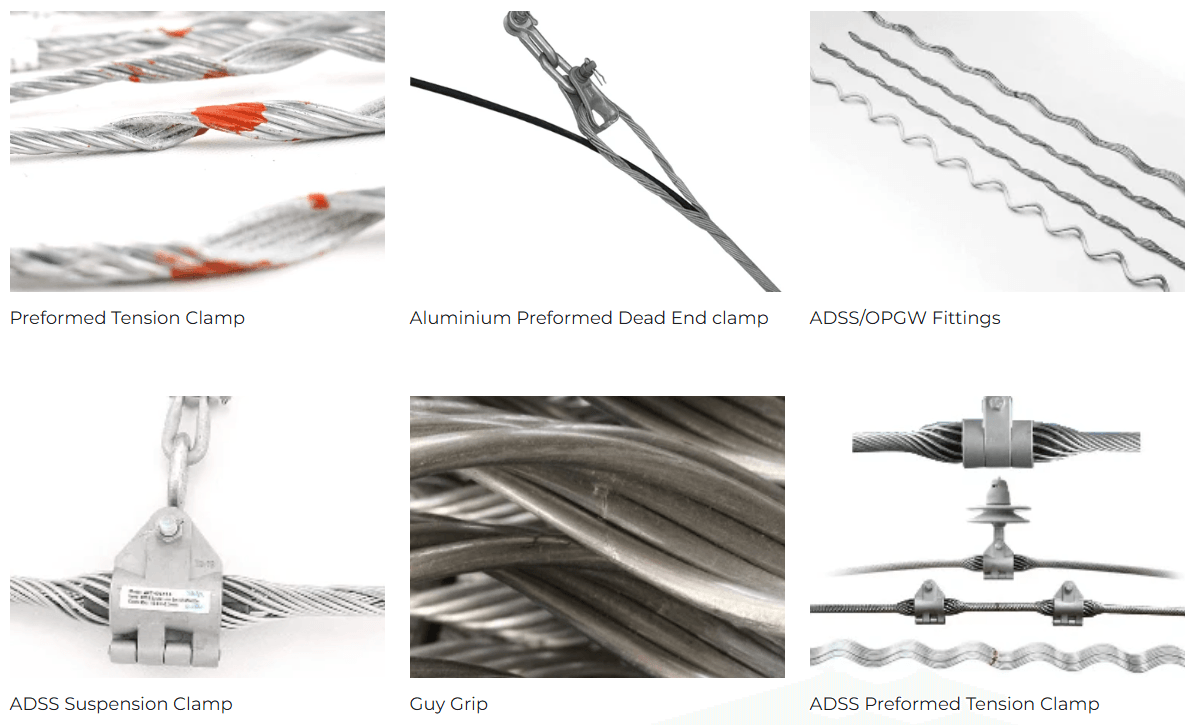
Selecting the right manufacturer for wire forms is crucial for ensuring quality and reliability in your projects. With numerous transmission wireform manufacturers in the market, it’s essential to evaluate each one carefully. By considering factors such as experience, reputation, and production capabilities, you can make an informed decision that aligns with your specific needs.
Factors to Consider for Selection
When evaluating wire form manufacturers, start by examining their industry experience and expertise. A manufacturer with a strong track record is likely to understand the intricacies of wire form production and can provide valuable insights into design and application. Additionally, consider their certifications and compliance with industry standards; this ensures that you’re partnering with a reliable supplier who prioritizes quality.
Another key factor is the range of materials offered by potential wire form suppliers. Different applications may require specific materials for optimal performance, so it's essential to choose a manufacturer that can accommodate these needs. Lastly, take into account their production capabilities—whether they can handle both small-scale orders and large-volume productions without compromising on quality.
Comparing Prices and Quality
Price is always a significant consideration when choosing between transmission wireform manufacturers; however, it should not be the sole deciding factor. While it’s tempting to go for the lowest price available, remember that quality often comes at a cost. Conduct thorough research on various wire form suppliers to understand how their pricing correlates with product quality—this will help you find a balance between affordability and reliability.
Requesting samples from different manufacturers can also aid in comparing quality directly. This hands-on approach allows you to assess not only material integrity but also craftsmanship in design and finishing touches of the wire forms produced by each supplier. Ultimately, weighing both price and quality will lead you toward making an informed choice that meets your project requirements.
Customer Support and Service Reliability
Excellent customer support is another critical aspect when selecting wire form manufacturers; after all, effective communication can save time and avoid costly mistakes down the line. Evaluate how responsive potential suppliers are during your initial inquiries—this will give you insight into their commitment to customer service throughout your partnership. Reliable support means you'll have assistance readily available should any issues arise during production or delivery.
Additionally, consider whether they offer post-sale services such as maintenance or troubleshooting advice for their products; this could significantly enhance your overall experience as a client. A manufacturer who stands behind their products through robust customer support demonstrates confidence in their offerings—a trait worth prioritizing when making your selection among various transmission wireform manufacturers.
Conclusion
In wrapping up our exploration of transmission wireform manufacturing, it’s clear that this sector is poised for exciting developments. As industries evolve and demand for custom wire forms increases, manufacturers must adapt to meet these needs effectively. The future is bright for wire form manufacturers who embrace innovation and quality.
The Future of Wire Form Manufacturing
The future of wire form manufacturing looks promising, driven by technological advancements and changing market demands. With the rise of automation and smart manufacturing processes, transmission wireform manufacturers are likely to enhance efficiency while maintaining high standards. This evolution will not only improve production rates but also allow for greater customization in wire forms to suit diverse applications.
Importance of Choosing Quality Suppliers
Choosing quality suppliers is crucial in the realm of wire forms, as it directly impacts product performance and overall project success. Reliable wire form suppliers ensure that their products meet stringent material specifications and design considerations, which can significantly affect durability and functionality. By prioritizing partnerships with reputable transmission wireform manufacturers, businesses can safeguard their investments and foster long-term growth.
Building Relationships with Manufacturers
Building strong relationships with manufacturers is a strategic move that can yield significant benefits over time. Collaborative partnerships with trusted wire form manufacturers facilitate better communication regarding design changes or production timelines, ultimately leading to enhanced product outcomes. Moreover, establishing rapport with key players in the industry fosters trust and reliability—essential ingredients for navigating the complexities of supply chains.