Introduction
CNC wire bending is a revolutionary process that has transformed the way metal components are shaped and formed. By utilizing advanced computer numerical control (CNC) technology, this method allows for the precise manipulation of wire into complex shapes and designs, making it an indispensable tool in various industries. As the demand for accuracy and efficiency grows, understanding CNC wire bending becomes even more crucial for manufacturers looking to enhance their production capabilities.
What is CNC Wire Bending
At its core, CNC wire bending involves using a CNC wire bending machine to automate the shaping of metal wires into desired configurations. This process not only streamlines production but also significantly reduces human error, ensuring each piece meets stringent quality standards. Whether it's a small CNC wire bending machine or a larger automated setup, these machines have become essential in producing everything from intricate brackets to robust structural components.
Importance of Precision in Metal Forming
Precision in metal forming cannot be overstated; it is vital for ensuring that parts fit together seamlessly and function as intended. In industries such as automotive and aerospace, even the slightest deviation can lead to catastrophic failures or costly rework. Therefore, investing in high-quality CNC wire bending machinery not only enhances product reliability but also boosts overall efficiency by minimizing waste associated with inaccuracies.
Overview of Wire Bending Machinery
Wire bending machinery comes in various forms, including manual wire bending machines for smaller operations and automated wire bending machines suited for high-volume production environments. Each type offers unique advantages depending on the scale of production and complexity of designs required. Understanding the differences between these machines can help manufacturers make informed decisions when evaluating CNC wire bending machine prices and features tailored to their specific needs.
Understanding CNC Wire Bending
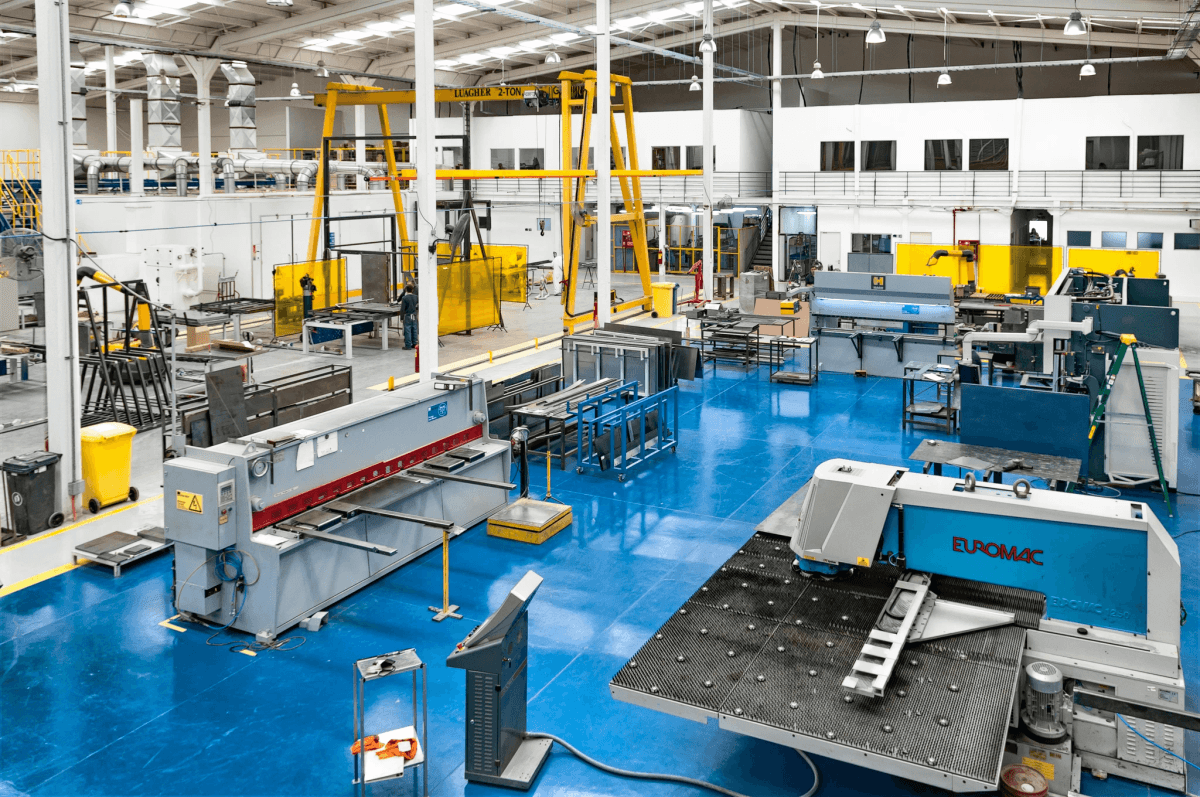
CNC wire bending is a cutting-edge process that utilizes computer numerical control technology to manipulate and shape wire into precise forms. This advanced method enhances the traditional wire bending techniques by automating the process, ensuring consistent quality and accuracy. Whether you're looking for a small CNC wire bending machine or a larger automated wire bending machine, understanding this technology is crucial for optimizing production.
Definition and Process
At its core, CNC wire bending involves using a CNC wire bending machine to bend metal wires into specific shapes according to programmed specifications. The process begins with inputting design parameters into the machine's software, which then controls motors to manipulate the wire accurately. This level of precision is unmatched by manual wire bending machines, making CNC technology a game-changer in manufacturing.
Key Benefits of CNC Technology
The key benefits of CNC technology in wire bending are manifold and can significantly impact production efficiency. First off, it drastically reduces human error compared to manual operations, leading to higher quality outputs with fewer defects. Additionally, investing in a small CNC wire bending machine can save time and labor costs while allowing for rapid prototyping and customization of designs—features that are invaluable in today’s fast-paced industries.
Common Applications in Industries
CNC wire bending finds applications across various sectors due to its versatility and precision. Industries such as automotive, aerospace, electronics, and furniture manufacturing rely heavily on this technology for creating intricate components quickly and efficiently. From producing brackets and frames to crafting custom fittings, the demand for automated wire bending machines continues to rise as companies seek innovative solutions that enhance productivity.
Types of CNC Wire Bending Machines
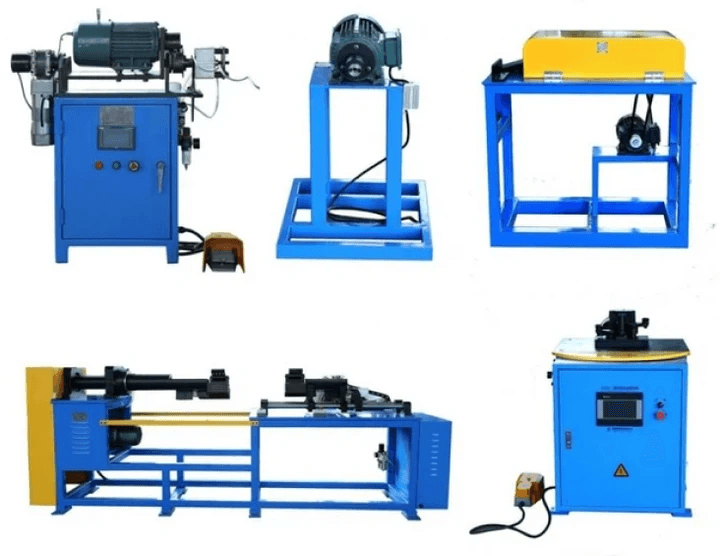
CNC wire bending machines come in various types, each suited for different applications and production needs. Understanding these types can help businesses make informed decisions when investing in their metal forming capabilities. Whether you're looking for a manual solution or an automated powerhouse, there's a CNC wire bending machine that fits the bill.
Manual Wire Bending Machines
Manual wire bending machines are the traditional approach to wire shaping, allowing operators to bend wire by hand using simple tools and techniques. While they may lack the precision of their CNC counterparts, these machines are often more affordable and accessible for small-scale operations or hobbyists. The manual wire bending machine is ideal for custom projects where flexibility and hands-on craftsmanship are paramount.
Despite their simplicity, manual machines require skilled operators who can produce consistent results through experience and practice. For those just starting in metal forming or looking to experiment with designs without hefty investments, this option is appealing due to its lower CNC wire bending machine price. However, as production demands increase, many find that transitioning to a small CNC wire bending machine becomes necessary for greater efficiency and accuracy.
Small CNC Wire Bending Machines
Small CNC wire bending machines bridge the gap between manual methods and full automation, offering enhanced precision while remaining compact enough for smaller workshops. These machines can handle various materials with ease and are designed to create complex shapes with minimal operator intervention. As businesses grow or diversify their product offerings, investing in a small CNC wire bending machine can significantly improve production capabilities.
One of the standout features of small CNC machines is their ability to be programmed easily for multiple bends without requiring extensive setup time between jobs. This versatility makes them a popular choice among manufacturers who need to produce custom parts quickly while keeping costs manageable—especially when considering overall cnc wire bending price advantages over larger systems. Additionally, these machines often come equipped with user-friendly software that simplifies design input and modifications.
Automated Wire Bending Machines
Automated wire bending machines represent the pinnacle of efficiency in modern metal forming processes, designed for high-volume production environments where speed and consistency are critical. These advanced machines utilize sophisticated programming and robotics to perform intricate bends with unparalleled precision—making them indispensable in industries such as automotive manufacturing or electronics assembly where tight tolerances are essential.
The investment required for automated systems tends to be higher compared to manual or small CNC options; however, the long-term benefits often outweigh initial costs when considering reduced labor expenses and increased output quality over time—especially relevant when evaluating cnc wire bending machine prices across different models. Furthermore, many automated systems integrate seamlessly with other manufacturing equipment, creating streamlined workflows that enhance productivity from start to finish.
In conclusion, whether you're opting for a manual solution out of necessity or seeking cutting-edge technology through automated systems, understanding your options will ensure you make an informed choice tailored to your specific needs in the world of cnc wire bending.
Choosing the Right CNC Wire Bending Machine
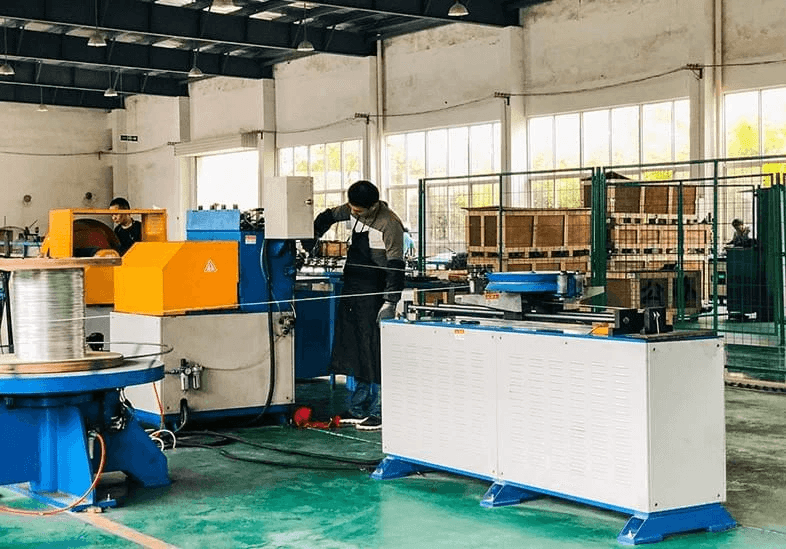
Selecting the right CNC wire bending machine is crucial for optimizing your production process. With a variety of options available, understanding the nuances of each type can significantly impact your efficiency and output quality. Whether you're considering a small CNC wire bending machine or an automated wire bending machine, making an informed decision will pay off in the long run.
Factors Influencing CNC Wire Bending Machine Price
The price of a CNC wire bending machine can vary widely based on several factors, including its capabilities and features. For instance, manual wire bending machines are generally more affordable but may lack the precision and speed of their automated counterparts. Additionally, advanced features such as programmable controls or integrated labeling systems can elevate the CNC wire bending price significantly.
Moreover, brand reputation and warranty offerings also play a role in determining costs. Investing in a reputable manufacturer may initially seem more expensive but often leads to better long-term reliability and support. Ultimately, balancing your budget with desired features is essential for finding the best fit for your manufacturing needs.
Comparing Features and Performance
When comparing different models of CNC wire bending machines, it's vital to look at key features that align with your production goals. For example, some small CNC wire bending machines might offer compact designs suitable for limited spaces while still delivering impressive performance metrics like speed and accuracy. In contrast, larger automated wire bending machines may provide greater throughput but require more floor space.
Performance metrics such as cycle time, bend accuracy, and material versatility should be prioritized during comparison shopping. Additionally, consider software capabilities; user-friendly interfaces can drastically reduce training time for operators while enhancing overall productivity. By weighing these factors carefully against your specific requirements, you can make an informed choice that meets both current demands and future growth potential.
Evaluating Manufacturing Needs
Before committing to any CNC wire bending machine purchase, it's essential to evaluate your manufacturing needs thoroughly. Start by assessing production volume—if you're producing high quantities regularly, investing in an automated wire bending machine could save you time and labor costs over manual alternatives. Conversely, if you have lower volumes or varied product designs to create frequently, a small CNC wire bending machine might be more appropriate.
Additionally, consider the types of materials you'll be working with; certain machines perform better with specific metals or gauges than others do. Don't forget about scalability—selecting machinery that allows easy upgrades or expansions will ensure you're prepared for future changes in demand without needing complete replacements down the line. Ultimately, aligning your equipment choice with both current operations and anticipated growth is key to maximizing efficiency.
Spark Fittings: Innovating Wire Bending Solutions
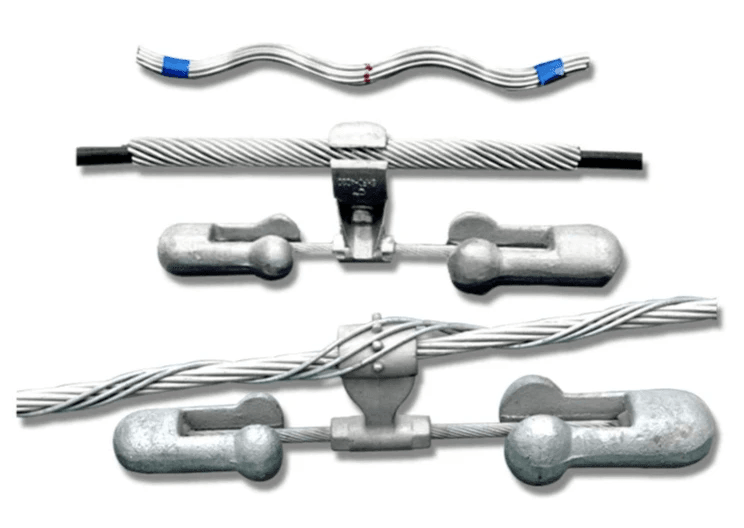
In the realm of CNC wire bending, innovation is key to staying ahead of the competition. Spark Fittings has taken a significant leap forward with their Twisted Wire Folding Labeling Machine, designed specifically for enhancing efficiency in wire bending processes. This machine not only streamlines production but also integrates seamlessly with existing setups, making it a game-changer for those utilizing CNC wire bending technology.
Twisted Wire Folding Labeling Machine Overview
The Twisted Wire Folding Labeling Machine from Spark Fittings is engineered to optimize the labeling process for various wire products. This machine combines advanced CNC wire bending techniques with innovative labeling features, ensuring that each piece is accurately folded and labeled without manual intervention. By automating these processes, manufacturers can significantly reduce labor costs and increase output rates while maintaining high precision.
This machine stands out among other options like manual wire bending machines and small CNC wire bending machines due to its versatility and speed. With a focus on user-friendly operation, it allows operators to easily set up and adjust parameters for different production runs. As industries continue to demand higher efficiency, this machine meets those needs head-on.
Features of the Twisted Wire Integration
One of the most notable features of the Twisted Wire Folding Labeling Machine is its ability to handle various types of materials with precision. It employs advanced sensors that ensure accurate positioning during the folding and labeling stages, which reduces waste and enhances product quality in CNC wire bending applications. Additionally, it offers customizable settings tailored to specific manufacturing needs—whether you’re using an automated wire bending machine or a small CNC wire bending machine.
Moreover, its robust design ensures longevity in demanding environments while requiring minimal maintenance compared to traditional manual wire bending machines. The integrated software allows for easy updates and modifications as production demands change over time, keeping your operations at peak performance levels without incurring excessive CNC wire bending price increases.
Benefits of Automated Labeling in Production
Automated labeling through machines like Spark Fittings' Twisted Wire Folding Labeling Machine brings numerous benefits to production lines engaged in CNC wire bending tasks. First and foremost is the drastic reduction in human error; automation ensures that every label is applied correctly every time—something that can be challenging with manual methods or even small CNC wire bending machines when dealing with high volumes.
Furthermore, automating this aspect frees up valuable labor resources that can be redirected towards more complex tasks within manufacturing processes. The resulting increase in productivity means businesses can scale operations without necessarily increasing overhead costs associated with hiring more staff or investing heavily in additional equipment like automated wire bending machines.
Finally, integrating such technology not only enhances operational efficiency but also positions companies favorably against competitors who may still rely on outdated methods or equipment—a critical factor given today's fast-paced market dynamics where CNC wire bending plays a pivotal role.
Maintenance Tips for CNC Wire Bending Machines
Maintaining your CNC wire bending machine is crucial for ensuring its longevity and optimal performance. Just like any sophisticated piece of machinery, regular upkeep can prevent costly downtimes and enhance precision in metal forming tasks. Here are some essential maintenance tips to keep your CNC wire bending equipment running smoothly.
Regular Inspection and Cleaning
Regular inspection and cleaning of your CNC wire bending machine should be at the top of your maintenance checklist. Dust, debris, and metal shavings can accumulate over time, potentially affecting the accuracy of bends made by both small CNC wire bending machines and larger automated wire bending machines. A thorough cleaning not only enhances performance but also helps identify wear and tear early on, preventing more significant issues down the line.
Make it a habit to inspect critical components such as the bending tool, clamps, and drive systems for signs of damage or misalignment. Additionally, lubricating moving parts will ensure they operate smoothly and reduce friction-related wear. Keeping a clean workspace around your manual wire bending machine or automated systems also contributes significantly to overall efficiency.
Importance of Software Updates
In today’s digital age, software plays a pivotal role in the operation of CNC wire bending machines. Regular software updates are essential to ensure that your machine operates with the latest features and improved functionalities that can enhance productivity. Ignoring these updates may lead to outdated processes that could affect both performance and precision.
Moreover, many modern small CNC wire bending machines come equipped with advanced software that aids in optimizing designs for better material usage and reduced waste. Staying current with software not only improves operational efficiency but also helps you stay competitive in an evolving market where precise bends are paramount. Remember: outdated software is like trying to bend metal with a rubber band—frustrating!
Troubleshooting Common Issues
Even with regular maintenance, issues can arise with any CNC wire bending machine from time to time—whether it’s a manual model or an automated system. Familiarizing yourself with common problems can save you valuable time when things go awry; for instance, if you notice inconsistent bends or unusual noises during operation, it’s essential to troubleshoot immediately rather than wait for disaster to strike.
Start by checking alignment settings; misalignments are often responsible for poor-quality bends across all types of machines—manual or automated alike! If problems persist despite adjustments, consulting the user manual may provide insights into specific error codes or troubleshooting steps unique to your model. In some cases, reaching out to customer support might be necessary; after all, even the best machinery needs a little TLC now and then!
Conclusion
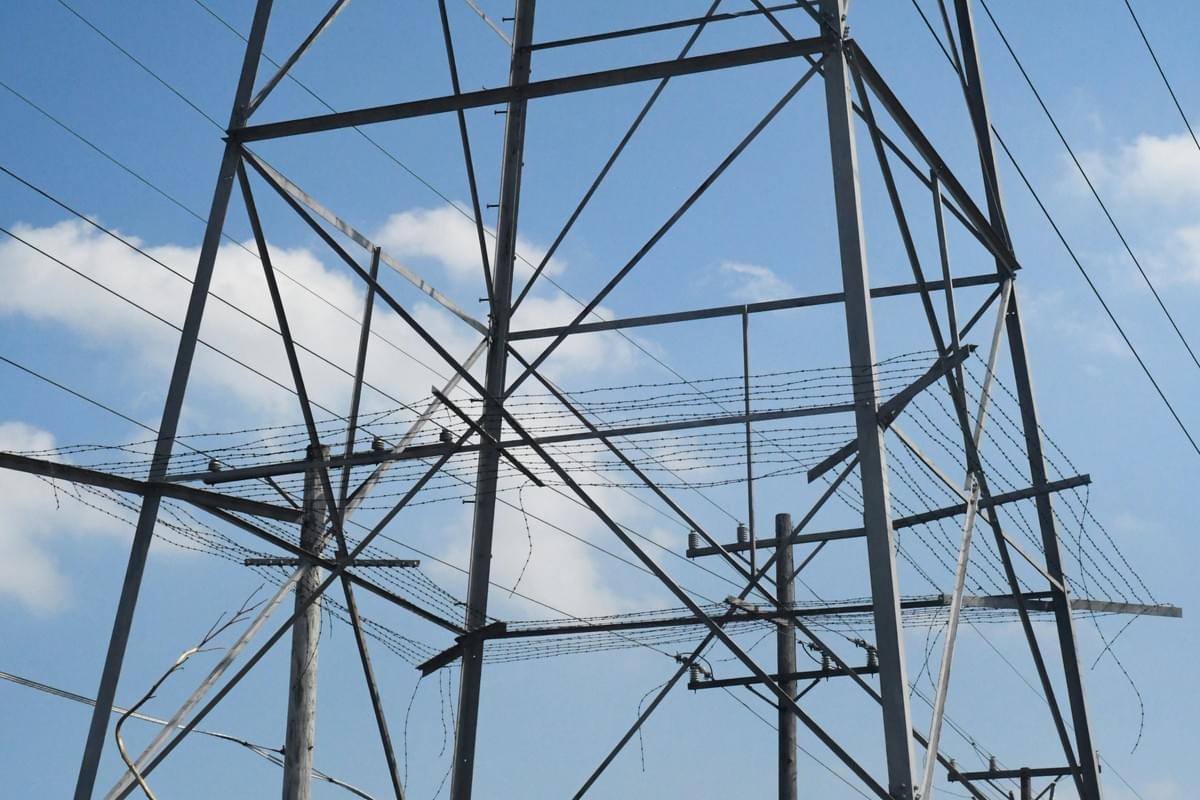
In the world of manufacturing, CNC wire bending stands out as a game-changer, providing unparalleled precision and efficiency. The integration of CNC technology into wire bending processes not only enhances productivity but also ensures that products meet stringent quality standards. As industries continue to evolve, embracing CNC wire bending machines becomes essential for staying competitive.
Maximizing Efficiency with CNC Technology
CNC wire bending technology revolutionizes how metal is shaped and formed, allowing manufacturers to produce intricate designs with remarkable accuracy. By utilizing a small CNC wire bending machine, businesses can achieve faster production times while minimizing waste. This efficiency translates into cost savings, making it a no-brainer for companies looking to optimize their operations.
Investing in Quality Wire Bending Machines
When considering the CNC wire bending machine price, it's crucial to weigh the long-term benefits against the initial investment. High-quality machines may come with a higher upfront cost but often lead to reduced operational issues and longer lifespans compared to manual wire bending machines or lower-tier models. Investing in an automated wire bending machine can also enhance production capabilities and provide better returns over time.
Future Trends in Metal Forming and Bending
The future of metal forming and bending is bright, with advancements in technology paving the way for even more innovative solutions in CNC wire bending. Expect to see smarter machines equipped with AI-driven analytics that optimize performance based on real-time data, pushing the boundaries of what small CNC wire bending machines can achieve. As industries adapt to these changes, understanding evolving trends will be key for manufacturers aiming to stay ahead of the curve.