Introduction

Exploring Galvanized vs Non Galvanized Nails
Galvanized nails are coated with a layer of zinc, which provides excellent corrosion resistance, making them ideal for outdoor use or in environments prone to moisture. In contrast, non-galvanized nails lack this protective coating, rendering them more vulnerable to rust and decay over time. By understanding the differences between these two types of nails, you can make an informed decision that best suits your project requirements.
Importance of Choosing the Right Nail
Choosing the right nail isn't just about aesthetics; it has practical implications for durability and performance. Using galvanized nails in situations where moisture is present can prevent costly repairs down the line due to corrosion-related failures. Conversely, non-galvanized nails may be adequate for indoor applications where exposure to water is minimal, thus saving costs without sacrificing quality.
The Basics of Nail Material Composition
The composition of both galvanized and non-galvanized nails plays a crucial role in their performance characteristics. Galvanized nails typically consist of steel coated with zinc through processes like electro galvanization or hot-dipping; this coating enhances their resistance to rusting significantly. Non-galvanized nails are generally made from plain steel without any protective layer, making them more susceptible to environmental factors that lead to deterioration over time.
Understanding Galvanized Nails
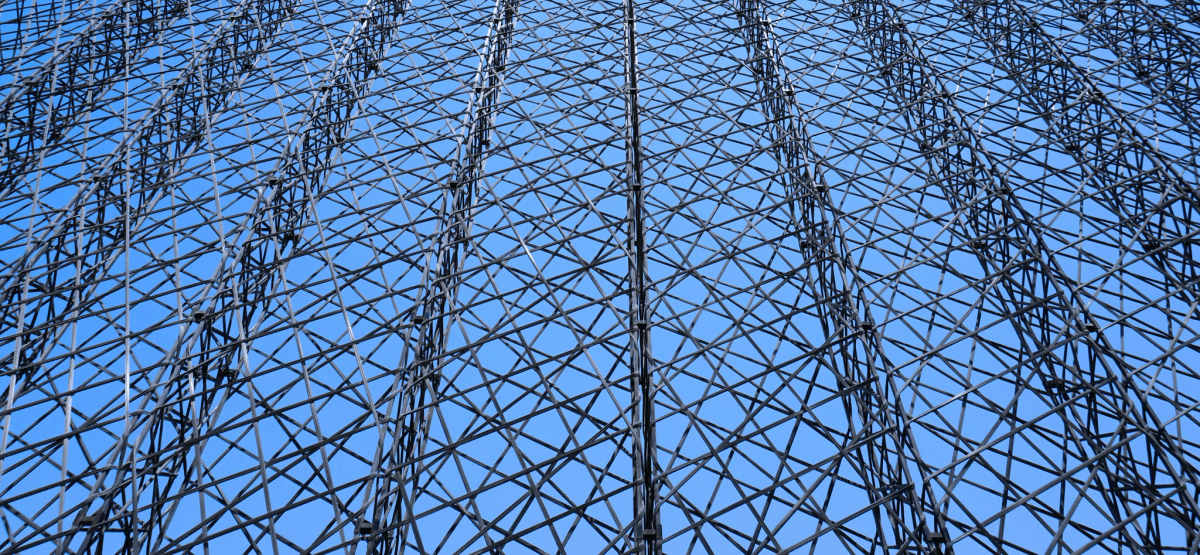
Definition and Composition of Galvanized Nails
Galvanized nails are steel fasteners that have undergone a process called galvanization, where they are coated with zinc to create a protective barrier against rust and corrosion. This coating can be achieved through various methods, including hot-dipping or electro-galvanizing—both effective in enhancing durability. The key difference between galvanized vs non-galvanized nails lies in this protective layer; while non-galvanized steel may succumb to rust quickly in humid conditions, galvanized nails can withstand such environments much better.
Common Uses for Galvanized Nails
So what are galvanized nails used for? Their robust nature makes them suitable for outdoor projects like decking, fencing, and roofing where moisture exposure is inevitable. Additionally, they are commonly used in construction settings such as framing—particularly galvanized framing nails—as well as in pressure-treated lumber applications due to their superior resistance against decay and corrosion compared to non-galvanized alternatives.
Advantages of Using Galvanized Nails
The benefits of using galvanized nails extend beyond just corrosion resistance; they also offer enhanced longevity and performance under challenging conditions. One major advantage is their ability to maintain structural integrity over time without succumbing to rust—a critical factor when considering the durability of any project involving wood or metal connections. Furthermore, when comparing what is the difference between galvanized and coated nails, it's important to note that while both provide some level of protection against rusting, galvanized nails typically offer greater resilience due to their thicker zinc coating.
The Scoop on Non Galvanized Nails
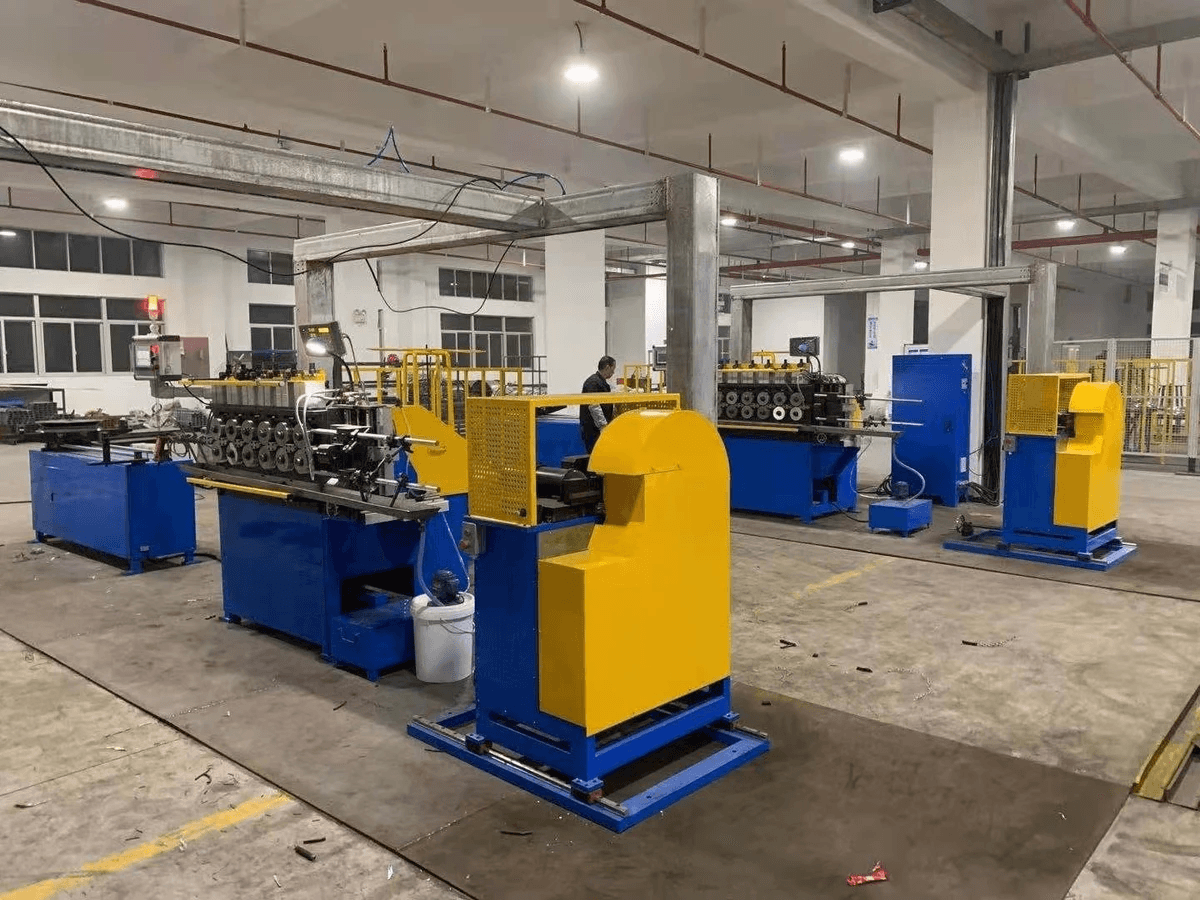
What are Non Galvanized Nails?
Non galvanized nails are simply steel nails that do not undergo any galvanization process. They are often used in applications where exposure to moisture is minimal, allowing them to perform adequately without the need for extra protection. However, it’s crucial to note that these nails can rust quickly when exposed to water or high humidity, making them less durable than their galvanized counterparts.
Standard Applications for Non Galvanized Nails
These nails find their primary use in indoor projects or dry conditions where moisture isn't a concern. Common applications include light framing, interior trim work, and attaching drywall where humidity levels remain stable. Unlike galvanized framing nails, which excel in outdoor settings due to their corrosion resistance, non galvanized options serve well in more controlled environments.
Disadvantages of Non Galvanized Nails
While non galvanized nails have their place in construction and DIY projects, they come with significant drawbacks compared to galvanized vs non galvanized nails. One major disadvantage is their susceptibility to rust; even a little moisture can lead to deterioration over time. Additionally, because they lack the protective coating found on electro galvanized nails or hot-dipped variants, they may not hold up well under varying temperatures or harsh conditions—making them a less viable option for long-term use.
What is the Difference Between Galvanized and Non Galvanized Steel?
Corrosion Resistance in Steel
Corrosion resistance is a key factor when comparing galvanized vs non galvanized nails. Galvanized steel undergoes a coating process that protects it from rust and other forms of corrosion, making it ideal for outdoor or high-moisture environments. In contrast, non galvanized nails lack this protective layer, which means they are more susceptible to rusting when exposed to moisture or harsh conditions.
This difference in corrosion resistance leads to distinct applications for each type of nail. For instance, what are galvanized nails used for? They are commonly employed in roofing, fencing, and other outdoor projects where exposure to moisture is inevitable. Non galvanized nails might be suitable for indoor projects where humidity levels are controlled but can lead to issues if used outside.
Cost Factors for Galvanized vs Non Galvanized Steel
When considering costs associated with these materials, there are notable differences between galvanized vs non galvanized steel as well. Generally speaking, electro galvanized nails tend to be less expensive than their hot-dipped counterparts due to simpler manufacturing processes; however, they may offer lower corrosion resistance compared to hot-dipped galvanization methods. Non galvanized options usually come at a lower upfront cost but may require additional maintenance or replacement over time due to their susceptibility to rust.
These cost factors can influence project budgets significantly—especially if you're working on large-scale endeavors like framing with galvanized framing nails versus using cheaper non-galvanized alternatives that might not hold up as well over time. Therefore, understanding these financial implications can guide you toward making more informed decisions about your material selections.
Durability in Varying Conditions
Durability is another critical area where the differences manifest themselves clearly when discussing what is the difference between galvanized and coated nails versus their non-galvanized counterparts. Galvanized nails typically exhibit superior durability under varying environmental conditions thanks to their protective coating that resists moisture penetration and oxidation effectively. On the other hand, non-galvanized nails may deteriorate quickly when exposed to elements such as rain or humidity.
In practical terms, this means that while you might save money initially by opting for non-galvanized options for certain projects—like indoor furniture assembly—you could end up spending more down the line if they fail prematurely due to corrosion-related issues. Thus, selecting the right type of nail based on your specific conditions will ultimately contribute significantly toward achieving long-lasting results in both residential and commercial applications.
Comparing Galvanized vs Non Galvanized Nails
Performance in Different Environments
The performance of galvanized vs non galvanized nails can vary significantly depending on the environment in which they are used. Galvanized nails are coated with a layer of zinc, enhancing their corrosion resistance, making them ideal for outdoor projects or areas with high humidity. In contrast, non galvanized nails may rust quickly when exposed to moisture, limiting their use primarily to dry indoor environments or temporary structures.
Understanding what are galvanized nails used for is essential; they excel in applications like roofing, siding, and decks where exposure to the elements is a concern. On the other hand, non galvanized options are often suitable for interior framing or furniture assembly where moisture levels are controlled. Ultimately, choosing between these two types boils down to assessing the specific conditions of your project site.
Longevity of Each Nail Type
Longevity is another critical factor when comparing galvanized vs non galvanized steel in nail form. Galvanized framing nails can last significantly longer due to their protective zinc coating that shields them from rust and decay over time. This durability makes them a popular choice among builders looking for long-lasting solutions that withstand various weather conditions.
Conversely, non galvanized nails have a shorter lifespan as they lack this protective layer; they may begin deteriorating within months if exposed to moisture or harsh environmental factors. Therefore, if you're planning a project that requires longevity and resilience—especially outdoors—galvanized options should be at the forefront of your selection process. Remember that investing in quality materials now can save you from costly repairs down the line.
Aesthetics and Finish Options
Galvanized nails typically have a shiny surface due to their zinc coating; this can add an appealing touch when visible in finished work like decking or siding installations. However, some might prefer the understated look of non galvanized nails which often blend seamlessly into wooden surfaces without drawing attention.
Additionally, both types come in various finishes such as electro-galvanized options that provide different levels of sheen and protection compared to hot-dipped alternatives known for their thicker coatings but rougher texture. If you're asking yourself what is the difference between galvanized and coated nails? The answer lies primarily in how much protection each offers against corrosion while still maintaining aesthetic appeal—coated options can sometimes provide better looks with adequate durability depending on specific needs.
In conclusion, whether you're choosing between electro-galvanized or traditional hot-dipped varieties—or even weighing your options with non-galvanized selections—considering performance in different environments and longevity will guide you toward making an informed decision tailored specifically for your project's requirements.
Electro Galvanized Nails vs Hot-Dipped Galvanized Nails
Manufacturing Processes Explained
Electro galvanized nails undergo a process where a thin layer of zinc is applied through electroplating, which is essentially a method of depositing metal ions onto a surface using electric current. This results in a shiny finish but offers less corrosion resistance compared to hot-dipped galvanized nails. On the other hand, hot-dipped galvanized nails are submerged in molten zinc, creating a thicker coating that provides superior protection against rust and corrosion—ideal for outdoor use or in damp environments.
Understanding what is the difference between galvanized and coated nails also plays an important role here; while both provide some level of protection against rust, hot-dipped galvanization offers much more robust defense due to its thicker coating. Consequently, this makes hot-dipped options more suitable for heavy-duty applications where longevity is critical. In contrast, electro galvanized nails might be preferred for indoor projects or situations where aesthetics take precedence over extreme durability.
Peak Performance Applications
When evaluating what are galvanized nails used for, it becomes clear that each type has its niche applications based on performance needs. Electro galvanized nails work well in environments that are not exposed to harsh conditions; they're often used in interior framing or light construction projects where moisture levels remain low. However, when you need something tougher—like with outdoor decking or roofing—the choice leans heavily toward hot-dipped galvanized framing nails due to their enhanced corrosion resistance.
In terms of performance under stress and exposure to elements like rain or snow, hot-dipped options shine brightly as they resist rust far better than their electro counterparts. This makes them ideal for construction projects that demand durability over time without compromising structural integrity. Knowing how these differences play out can assist you in making smarter decisions about which type to use based on your specific project requirements.
Quality and Price Analysis
Quality often correlates with price when distinguishing between electro galvanized vs non-galvanized steel products; generally speaking, you’ll find that hot-dipped galvanization commands a higher price point due to its superior protective qualities and longer lifespan. However, this investment pays off by reducing maintenance costs over time since you'll be less likely to replace corroded fasteners frequently compared to cheaper alternatives like electro-galvanized options.
While the initial cost may deter some buyers from opting for high-quality hot-dipped options right away, considering long-term value reveals why many professionals prefer them despite higher upfront expenses—especially when working on projects requiring reliability under challenging conditions. Ultimately, weighing quality against price will help you decide whether investing in durable solutions pays off in your specific scenario.
Best Practices in Nail Selection
Choosing the right nails for your project can make all the difference between a sturdy structure and a shaky one. When it comes to galvanized vs non galvanized nails, understanding their unique properties is crucial. Factors such as environmental conditions, material compatibility, and intended use should guide your decision-making process.
Factors to Consider When Choosing Nails
First and foremost, consider the environment where the nails will be used. If you're working on an outdoor project or in a humid area, galvanized nails are often preferred due to their corrosion resistance. Additionally, think about what is the difference between galvanized and coated nails; while both offer protection against rust, coatings can vary significantly in durability and application suitability.
Next up is the type of materials you'll be fastening together. Different materials may require specific types of nails for optimal performance; for instance, using galvanized framing nails in wood structures ensures longevity without compromising strength. Lastly, budget considerations are essential—galvanized vs non galvanized steel can differ greatly in price due to manufacturing processes and material treatments.
Recommendations for Specific Projects
For outdoor constructions like decks or fences, always opt for galvanized nails due to their ability to withstand moisture and prevent rusting over time. Similarly, if you're working with treated lumber—which often contains chemicals that can corrode non-galvanized steel—galvanized options are a must-have. On the other hand, if you’re tackling indoor projects where aesthetics matter more than corrosion resistance (like cabinetry), non-galvanized nails might suffice.
When dealing with heavy-duty applications or structural framing work, using galvanized framing nails ensures that your construction remains solid under stress conditions. For light-duty tasks such as hanging pictures or assembling furniture indoors, non-galvanized options could do just fine without breaking the bank.
How Spark Electronic Technology Relates to Nail Selection
Spark Electronic Technology Wuxi Co., Ltd., while primarily focused on manufacturing equipment for electrical components like preformed armor rods and tension clamps, demonstrates how technology enhances product quality across industries—including nail production! Their advanced machinery ensures that products meet high standards of durability and reliability—qualities you want in any fastener you choose.
Moreover, understanding how electro galvanized nails are produced can shed light on why they might be suitable for certain applications compared to hot-dipped options. Their expertise highlights how precision engineering not only applies to electrical accessories but also influences nail performance—ultimately impacting your choice between galvanized vs non galvanized nails based on project needs.
Conclusion
In wrapping up our exploration of galvanized vs non galvanized nails, it’s clear that each type has its unique advantages and applications. Galvanized nails are coated with a protective layer that enhances their resistance to corrosion, making them ideal for outdoor or moisture-prone environments. On the other hand, non galvanized nails are suitable for dry indoor projects where rust is less of a concern.
Summary of Key Differences
When considering what is the difference between galvanized and non galvanized steel, the primary distinction lies in their treatment; galvanized nails undergo a zinc coating process that protects against rust and degradation, while non galvanized nails do not have this protective layer. Additionally, when we ask what is the difference between galvanized and coated nails, it's important to note that coated nails may use various materials for protection but lack the robust coverage provided by galvanization. Ultimately, understanding these differences helps in selecting the right nail type based on specific project needs.
When to Use Galvanized vs Non Galvanized Nails
Galvanized nails are best utilized in scenarios where moisture exposure is inevitable—think fencing, roofing, or outdoor furniture projects—where durability is paramount. Conversely, if you're working on an interior project like framing or cabinetry where humidity levels are controlled and low risk of corrosion exists, non galvanized nails will do just fine without breaking the bank. Remembering what are galvanized nails used for can save you time and money in choosing the right fasteners for your tasks.
Final Thoughts on Nail Selection and Quality
Choosing between galvanized vs non galvanized steel boils down to understanding your project's environment and requirements. Electro galvanized nails offer a lighter coating than hot-dipped options but can still provide adequate protection in less demanding conditions; thus knowing your application can greatly influence your choice between these types of fasteners. Whether you’re opting for robust Galvanized Framing Nails or lighter alternatives, always consider how Spark Electronic Technology Wuxi Co., Ltd.'s innovative equipment can contribute to producing high-quality products tailored for specific applications.